EDIT BATACLO :
Je voudrais apporter une remarque préliminaire à ce reportage de Philippe.
Philippe nous fait le plaisir et le privilège de nous livrer son compte rendu de visite de l'usine BENETEAU, je le remercie sincèrement pour ce travail personnel.
Vous qui êtes membres de VCF et/ou qui nous lisez régulièrement, vous savez que sur VCF notre fierté c'est le partage de notre passion pour le nautisme et son environnement.
Votre pratique de notre site, vous permet aussi de savoir que nous sommes attachés à la liberté de ton et d'expression.
Philippe me reprendra au besoin, mais il n'a pas omis de signaler à ses interlocuteurs les réticences portant sur les contrôles qualités, émises par divers propriétaires de bateaux neufs de ce groupe. Aussi je tiens au nom du forum à remercier les responsables de cette firme pour cette volonté de transparence et demande à chacun de RESPECTER ce fil de discussion.
ClaudeCe fil de discussion n'engage que moi, mais j'ai tenu à le partager avec vous, bonne lecture!
Suite aux problèmes rencontrés par quelques membres du forum ou des connaissances, après la commande de notre A8OB je me suis débrouillé pour pouvoir visiter l’usine de fabrication de BENETEAU au POIRE sur Vie.
J’ai été accueilli par Mr Gildas REHEL Technico commercial qui nous a guidés tout au long de cette visite et nous avons été reçus en fin de visite par Mr Michel BUSSIERE Directeur Qualité Plaisance Groupe BENETEAU.
Mr REHEL connaît bien ses produits et mode de fabrication, il lui est arrivé et lui arrive encore d’intervenir en SAV sur des cas particuliers.
Mr BUSSIERE a pris ses fonctions il y a neuf mois et vient du milieu aéronautique que je connais particulièrement bien. (Il a 25 ans d’expérience) Son ancien employeur était un de nos clients et nous avons quelques connaissances en commun.
Comme mentionné plus haut, je connais l’aéronautique, les chaînes de montage A320 – A380 et les chaînes d’assemblage moteurs, le nautisme restait pour moi à découvrir. Je peux vous dire que j’ai été très agréablement satisfait de tout ce que j’ai pu voir, commençons par le début :
L’usine du POIRE sur Vie :
A quelques kilomètres de la Roche sur Yon, cette usine réalise principalement des voiliers pour BENETEAU (OCEANIS) et JEANNEAU (SUN ODYSEY) ainsi que quelques catamarans type LAGOON.
Nous commençons la visite par le moulage des coques :
Bien évidement il y a les moules, minimum deux exemplaires pour faire face à la demande et en cas d’indisponibilité temporaire d’un moule.
L’usine du Poiré est tout à fait capable de vous fournir une coque d’un First si vous en avez besoin, les anciens moules sont stockés et maintenus en état.
Les deux méthodes de fabrication sont employées au Poiré, l’imprégnation et l’infusion.
L’avantage incontestable de l’infusion est l’absence d’odeurs (donc de nocivité), moins de COV et obtention de surfaces parfaitement finies (des deux côtés pour certaines pièces)
Les opérations de moulage sont réalisées en grande partie par des femmes (et oui, elles sont plus agiles et soigneuses que nous les hommes). Des fiches techniques précisant comment réaliser les coques sont disponibles aux postes de travail et précisent notamment comment placer les découpes de fibres de verre spécifiques (qui arrivent aux postes de travail déjà découpées par un laser et identifiées), le nombre de couches de fibres est aussi précisé…
Les monteurs ont juste à prendre les pièces de fibres déjà découpées et à les mettre en place et ajouter la résine et de la fibre avec un appareil équipé d’un pistolet, tout cela avec calme et professionnalisme.
Une fois la coque terminée, elle sèche, puis elle est démoulée.
Après le démoulage intervient le premier contrôle visuel de tout le gelcoat de la coque, à chaque imperfection le contrôleur (nous avons essentiellement vu des femmes au contrôle) appose une pastille de couleur sur l’indication qui sera ensuite reprise manuellement.
Il en est de même pour le moulage par infusion, sauf que pour le contrôle, en plus du visuel, un contrôle que j’appelle « Tap Test « et que je connais depuis 25 ans dans l’aéronautique permet sur des pièces en carbone des avions de déterminer les « délaminages » du composite. Ici au Poiré, c’est pareil, les contrôleurs utilisent une pige à bout arrondi pour tapoter dans les zones à défauts potentiels connus : si vous entendez une légère résonnance c’est conforme, si le bruit est étouffé, vous avez un défaut dessous (bulle d’air généralement), une pastille de couleur est apposée, une retouche manuelle sera effectuée.
Il en est de même pour les ponts réalisés dans un bâtiment voisin.
Une machine 5 axes pour l’ébarbage et les découpes.L’usine du Poiré dispose d’une salle fermée dans laquelle sont ébavurés, découpés ou percés les ponts (découpes des ouvertures…) Ce travail était réalisé manuellement auparavant dans des conditions difficiles pour les opérateurs qui devaient être équipés de scaphandre, c’est maintenant une immense « fraiseuse » 5 axes qui réalise ces opérations après avoir pris des points de repère sur le pont.
La coque et le pont passent ensuite dans un hall d’assemblage, dans ce hall les coques sont disposées à gauche et les ponts à droite.
A partir de ce stade, chaque pont / coque doit translater au poste suivant toutes les six heures.
Nous avons pu voir les premières opérations de montage réalisées sur la coque : pose de faisceaux électriques et tuyauteries d’eau froides et chaudes, pompes, ballon d’eau chaude…
Au poste suivant on pose le moteur etc. et ainsi de suite.
A chaque poste vous avez un contrôleur (toujours une femme) qui vérifie certains points suivant une check liste.
J’ai aussi observé que chaque opérateur avait ce que j’appelle « une fiche suiveuse » et qui précise les opérations à effectuer, une fois la tâche effectuée, l’opérateur vise la fiche ce qui atteste que l’opération a bien été réalisée, cela permet aussi de savoir par la suite qui a effectué cette opération si d’aventure on la trouve défectueuse.
Au fur et à mesure que l’on avance on voit l’installation des différents meubles et accessoires en commençant par la proue pour finir par l’arrière du bateau.
L’assemblage coque / pont :
Le moment est venu d’assembler le pont sur la coque ! un essai à blanc est réalisé, des retouches sont effectuées si nécessaire, puis c’est l’assemblage à l’aide d’une colle spécifique, de vis et de mastique d’étanchéité. (C’est juste après ce poste d’assemblage que Robert vient demander à Marcel s’il a pensé à sortir son sandwich au Maroilles qu’il avait placé dans la zone totalement inaccessible après assemblage du pont sur la coque ! LOL !)
Puis vient la piscine, uniquement pour tester l’étanchéité de la coque et des passes coque ainsi que certains équipements.
L’étape d’après est un contrôle approfondi de tout ce qui est visible et non visible : une contrôleuse est à quatre pattes avec sa lampe pour vérifier le dessous de la table de cockpit, les portes des meubles et toujours la pose de stickers si une anomalie est constatée. L’anomalie est enregistrée et communiquée afin qu’un opérateur intervienne pour la corriger, les stickers sont alors retirés, la fiche de retouche visée, on peut passer à l’étape suivante.
A ce stade vous avez aussi des tests d’étanchéité, comme pour le réseau de gaz par exemple.
L’étape suivante se passe dans un autre bâtiment près des expéditions, c’est à nouveau une piscine mais avec des asperseurs pour s’assurer que l’eau ne s’infiltre pas dans le bateau.
S’il n’y a pas de fuite le bateau est bon pour livraison, il ne reste plus qu’à le coconner et le stocker en attendant le camion.
En cas d’infiltration, une retouche de la zone incriminée est réalisée et nouveaux tests.
Il est rare de trouver des infiltrations à ce stade, l’expérience de fabrication ainsi que les retours des concessionnaires ou des clients sont pris en compte pour limiter au maximum les problèmes.
Formation :
En France, BENETEAU a son propre centre de formation, il est évident que beaucoup des métiers mis en œuvre chez ce constructeur n’ont pas de formation professionnelle ou scolaire.
Pour pallier à ce problème, BENETEAU a créé son propre centre de formation, pour former tous les opérateurs aux différents métiers de la construction et l’assemblage des bateaux.
Cette formation n’est pas acquise à vie, les opérateurs sont amenés à avoir une piqûre de rappel tous les trois ans ou moins si nécessaire.
Ce centre de formation est unique en France chez BENETEAU, les autres usines aux USA et en Pologne ne bénéficient pas de centre comme celui-ci. BENETEAU est en train de développer « un pont » entre l’école de formation et les usines situées aux USA. Il est à noter que ce centre de formation dépend du service Qualité de BENETEAU.
Entretien avec le Directeur Qualité, Mr Michel BUSSIERE :
Comme précisé plus haut, cela fait maintenant neuf mois que Mr BUSSIERE a intégré ce poste, il vient du monde de l’aéronautique.
Il est conscient comme tout Directeur Qualité qu’il y a des non conformités exportées et il a été décidé avec la Direction de travailler sur quelques axes d’amélioration :
- La qualité des fournisseurs
- Le respect des fiches de fabrication
- Les processus
- L’ébénisterie
- Le coût de non qualité usine, rebut, retours clients…
Non pas que ce n’est pas fait actuellement, mais la Direction avec la Qualité ont décidé de renforcer ces axes. Pour cela tous les Directeurs et Responsables Qualités sont mobilisés.
Directeurs Qualité usines, produits, fournisseurs et développement etc…
Mr BUSSIERE est conscient que des non conformités sont exportées chez les clients, certaines sont rapidement réglées par les concessionnaires, d’autres plus difficiles par les équipes du SAV.
Ensuite, il y a un très faible pourcentage de cas difficile à régler et à gérer au cas par cas.
Etant de la partie mais dans un autre domaine, je sais que dans un métier ou 95% du travail est réalisé par des opérateurs, le zéro défaut est difficilement atteignable. Pour obtenir ou tendre vers ce résultat, la formation des opérateurs et des contrôleurs est indispensable, entre autre.
Conclusions :
Nous avons été très agréablement surpris par le professionnalisme des employés de cette usine, leur amabilité (toutes les personnes que nous avons croisées nous ont systématiquement dit bonjour). Le personnel ne court pas, il connaît les tâches à réaliser, il a à sa disposition les outils et documents nécessaires pour l’exécution de ces dernières. Le travail et les contrôles sont réalisés avec précision et une maîtrise qui nous a marqué.
En ce qui nous concerne, nous membres du forum, nos bateaux sont réalisés à Ostroda, nous connaissons les problèmes rencontrés par certains d’entre nous sur des produits provenant de Pologne, c’est malheureusement indéniable et pourtant que ce soit BENETEAU ou les concessionnaires, tous disent qu’Ostroda est l’usine la plus moderne du groupe.
Je ne peux vous dire comment sont réalisé et contrôlés nos bateaux sortant de cette usine, il ne m’a pas été possible de la visiter.
Après, comme je l’ai précisé dans un autre post, il faut aussi comparer le nombre de problèmes par rapport au nombre de bateaux fabriqués, le groupe BENETEAU fabriquant beaucoup d’unités, il n’est peut-être pas anormal d’avoir un nombre de non-conformité important, même si c’est toujours trop.
Quelques photos fournies par BENETEAU car vous vous doutez qu’il est interdit de prendre des photos, il y a aussi un lien internet, en suivant ce lien vous pourrez voir la salle dans laquelle il y a l’immense 5 axes qui ébarbe et découpe les ponts.
http://www.beneteau.com/fr/construireOCEANIS YACHT 62.jpg
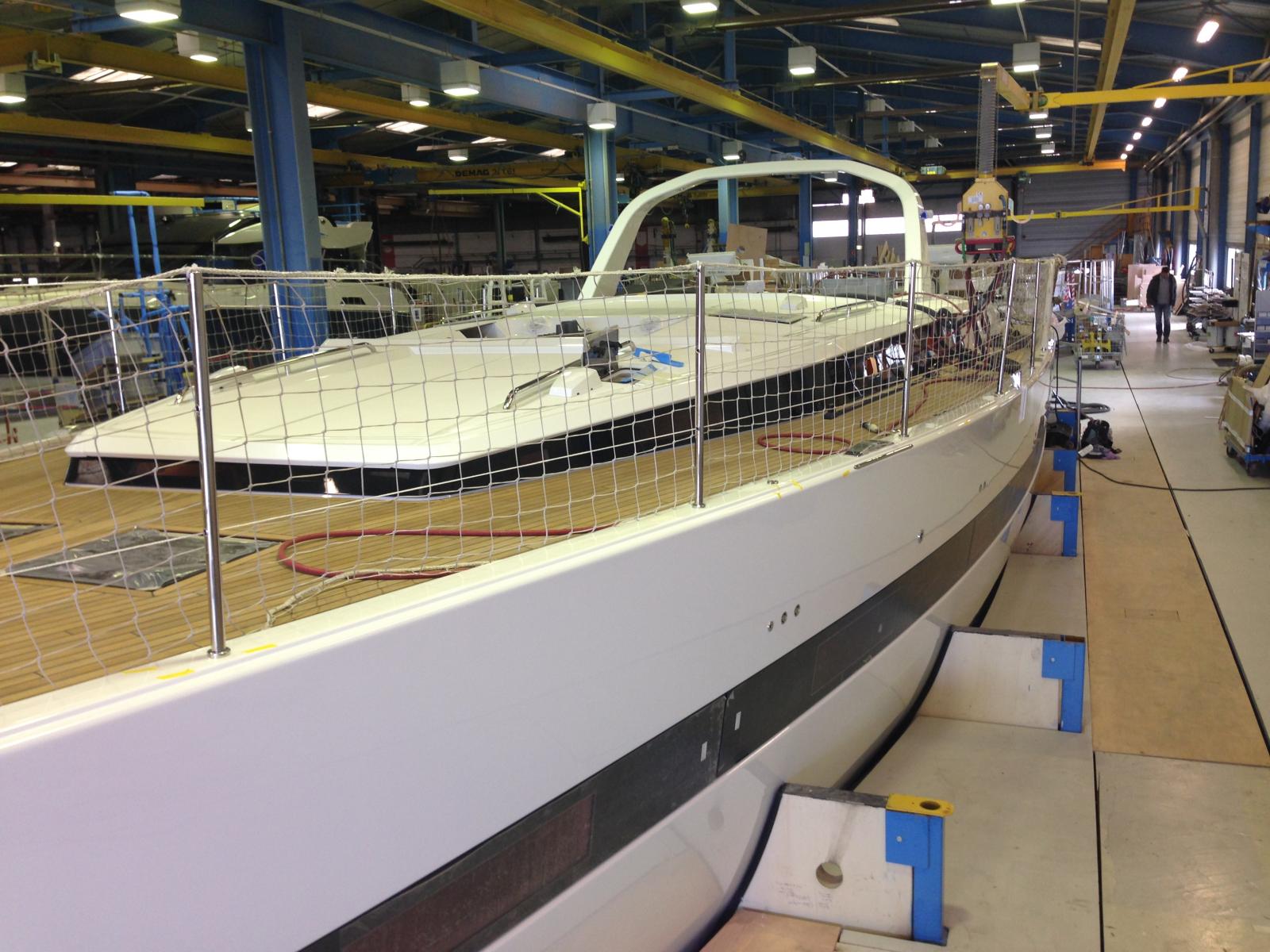
_MFA24318.jpg